Episode 56
Achieving Digital Transformation in the Electronics Manufacturing Industry
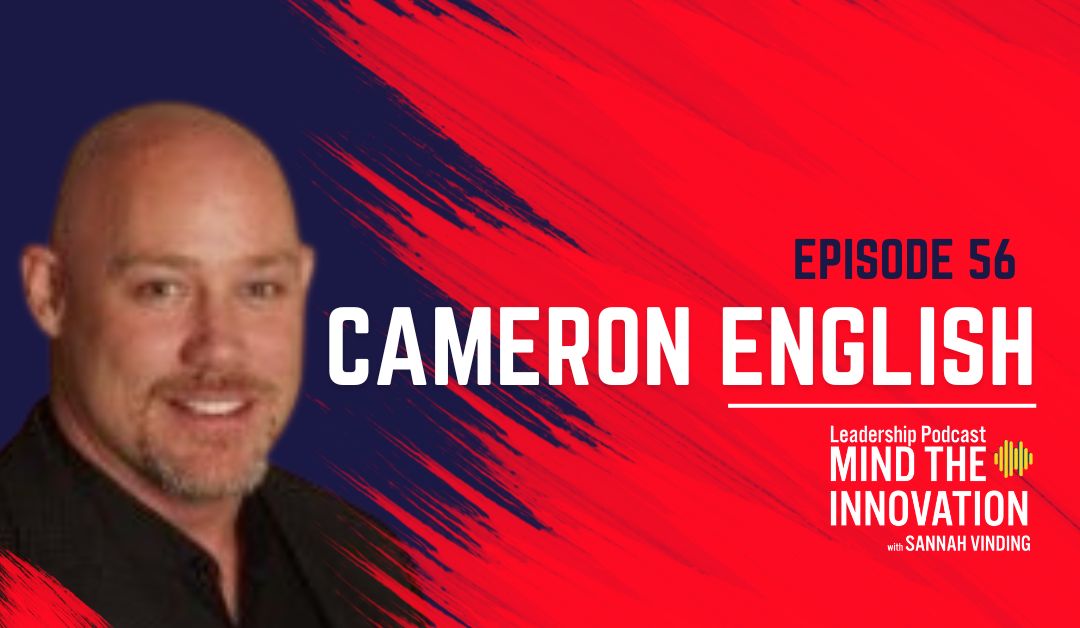
The electronics industry is constantly evolving, and the pace of change has only accelerated in recent years. With the advent of new technologies such as IoT, artificial intelligence, and machine learning, engineers are now required to have a more interdisciplinary skill set, which includes knowledge of software development, data analytics, and computer engineering, in addition to traditional mechanical and electrical engineering skills. But how can manufacturers and manufacturers reps serve engineers in the best way to keep up with the speed of development?
In this episode of the Mind The Innovation Leadership Podcast, Cameron English, President/CEO at English Technical Sales, joins the show to discuss how to grow and shape future strategies by creating an organizational culture. He will share his insights on how to foster an agile and resilient culture, the importance of investing in digital technologies, and how to empower employees to take ownership of their roles. The conversation will also delve into how to navigate disruptions and the impact of the COVID-19 pandemic on the industry. Listeners will gain valuable insights into how to build a culture that drives innovation and success in the fast-paced world of electronics manufacturing.
Host
Sannah Vinding
Guest
Episode
E56
Key takeaways



Despite the challenges, we emerged stronger as we were able to capitalize on the areas that were performing well by pivoting and refocusing our efforts.
Adapt to new ways of working
The COVID-19 pandemic has forced many manufacturing companies to adapt to new ways of working, including remote working and social distancing. This has led to a shift in the way that departments collaborate within manufacturing companies. Some of the reasons why collaboration between departments has evolved after the pandemic include:
- Remote working: With many employees working remotely, it has become more important for departments to collaborate and communicate effectively to ensure that projects and tasks are completed on time. Remote working has also increased the need for digital tools and platforms that enable teams to collaborate and share information remotely.
- Increased flexibility: With the pandemic, many manufacturing companies have had to adapt to changing customer demands and supply chain disruptions. This has led to a greater need for collaboration between departments to quickly respond to these changes.
- Improved communication: The need for remote working and social distancing has led to an increase in the use of digital communication tools, such as video conferencing and instant messaging. This has improved communication between departments and made it easier for teams to collaborate on projects.
- Data sharing: The pandemic has led to an increased need for data sharing between departments to track production and inventory levels, monitor supply chain disruptions, and respond to changing customer demands.
- Emphasis on digital transformation: The pandemic has accelerated the need for digital transformation within manufacturing companies, and this has led to a greater need for collaboration between departments to implement new technologies and processes.
Overall, the pandemic has driven manufacturing companies to adapt to new ways of working and this has led to an evolution of collaboration between departments to meet the challenges of the new scenario. Companies that can effectively collaborate across departments will be better equipped to navigate the challenges of the pandemic and position themselves for success in the future.
The pandemic has accelerated the need for digital communication tools, such as video conferencing and instant messaging, which has improved communication between departments and made it easier for teams to collaborate on projects.
Encourage and achieve digital transformation
Achieving digital transformation in an electronics manufacturing industry doesn’t just involve implementing technology-based solutions. It’s also essential to create a cultural environment that is conducive to change and innovative ideas. This means investing in the right training programs, creating the necessary infrastructure for innovation, and encouraging collaboration between departments and team members.
Creating this kind of culture starts with open communication among business leaders, managers, engineers, and other stakeholders. By fostering an environment based on trust and respect, teams can comfortably introduce new ideas without fear of critique or failure. Once that happens, it opens up opportunities to take riskier initiatives that have higher chances of success due to proper learning and planning mentality.
Additionally, investing in the right tools and resources is essential. Having access to high-quality software solutions can facilitate data collection and analysis which can be used to inform decisions taken by leadership or engineering personnel in order to improve efficiency or overall customer experience. That said, no matter how powerful these tools are they won’t be effective if they’re not used correctly; appropriate training needs to be available in order for them to be used correctly by all involved parties.
Manufacturers in the electronics industry need to stay competitive by investing in best-in-class technology, seeking out new distribution channels, staying up-to-date on changing customer needs, and maintaining a strong online presence. Having a professional website that provides consistent information about your products or services is essential for staying competitive.
Success in the new reality requires strong collaboration and coordination skills, including communication, multitasking, and fast project management. Organizations are increasingly adopting a collaborative approach to product development.
Cultural Shift
Achieving digital transformation is not just about implementing technological solutions, but also about creating a culture within an organization that fosters digital initiatives. In order for digital initiatives to succeed, there needs to be a cultural shift within the organization. This means that the organization needs to be open to change, willing to take risks, and ready to embrace new technologies and ways of working.
To foster this culture, organizations need to establish a clear digital strategy that aligns with their overall business goals. This strategy should be communicated to all employees and clearly outline the organization’s digital vision and objectives. It is also important for the organization to establish a digital governance structure that ensures that digital initiatives are aligned with the overall strategy and that they are implemented in a consistent and controlled manner.
It is important for organizations to invest in the right people and skills to support digital initiatives. This means hiring employees with the right technical skills and training existing employees to work with new technologies. Additionally, organizations should create a digital leadership team that has the authority and responsibility for driving digital initiatives forward.
Achieving digital transformation requires more than just implementing technological solutions. It requires a cultural shift within an organization that fosters the right environment for digital initiatives to succeed. This can be achieved by creating a clear digital strategy, establishing a digital governance structure, fostering a culture of innovation and experimentation, investing in the right people and skills, and establishing a digital leadership team
Investing in digital technologies
Investing in digital technologies is one of the most important aspects of digital transformation within the electronics manufacturing industry. Digital technologies provide a platform to optimize processes and develop innovative solutions, allowing organizations to be more agile and competitive.
Manufacturing companies that are investing in digital technologies, such as automation, machine learning, and the Internet of Things (IoT), as well as software/platforms like Autoklose, HubSpot, ZoomInfo, and LinkedIn Sales Navigator, are taking a step in the right direction to improve their operations. These technologies can help with sales and marketing strategies and processes, like automating lead generation, tracking customer interactions, and identifying new opportunities. By utilizing these digital technologies and software, manufacturing companies can stay competitive in an increasingly globalized marketplace, improve their overall performance and drive revenue growth.
Ultimately, when it comes to competing in today’s highly competitive industry space, having a clear understanding of what technology investments are needed is crucial. This requires a comprehensive assessment of current capabilities and an actionable roadmap for future investments. By leveraging the right digital strategies, an organization can ensure it is positioned for success now and in the future.
Cameron English
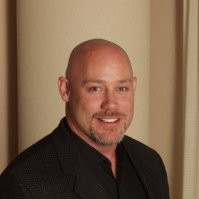
Cameron English
President/CEO at English Technical Sales
Manufacturers’ representative – Operating and managing a leading representative organization with 12 Sales Engineers in our Network, working with Hi-Tech Electronic products in a variety of Industry Segments.
My goal is to expand our organization to become a Value Add Sales Organization covering the Southwest United States Region.
Specialties: Specialize in Electromechanical Electonic Technology, managing and operating a Highly Skilled Sales team.
Related Episodes
How to Build Trust-Based Leadership: Lessons from oemsecrets.com Founder Sam Cowley – Episode 111
Join host Sannah Vinding on the Leadership In Manufacturing Podcast as she chats with Sam Cowley, founder of oemsecrets.com. Explore his insights on leadership, building partnerships, company culture, and mentorship in the electronics industry. Hear Sam’s journey from starting oemsecrets.com to forging global industry relationships. Perfect for anyone interested in leadership and growth in manufacturing!
What’s The Best Advice For New Leaders In Manufacturing? Episode 110
What Is the Best Advice for New Leaders in Manufacturing? Making decisions with confidence and seeing mistakes not as failures, but as opportunities to learn. Listen to the full episode
New Episodes
Bi-Weekly Tuesday